Partners
ECORES WIND brings together a consortium of industry leaders, academic institutions, and research organisations.
Our partners are at the forefront of innovation in wind energy, materials science, and circular economy practices.
The partnership includes chemical companies, composite manufacturers, and environmental scientists, all working collaboratively to achieve the project’s goals.
This multidisciplinary team will ensure a comprehensive approach to developing and implementing our circular solutions.
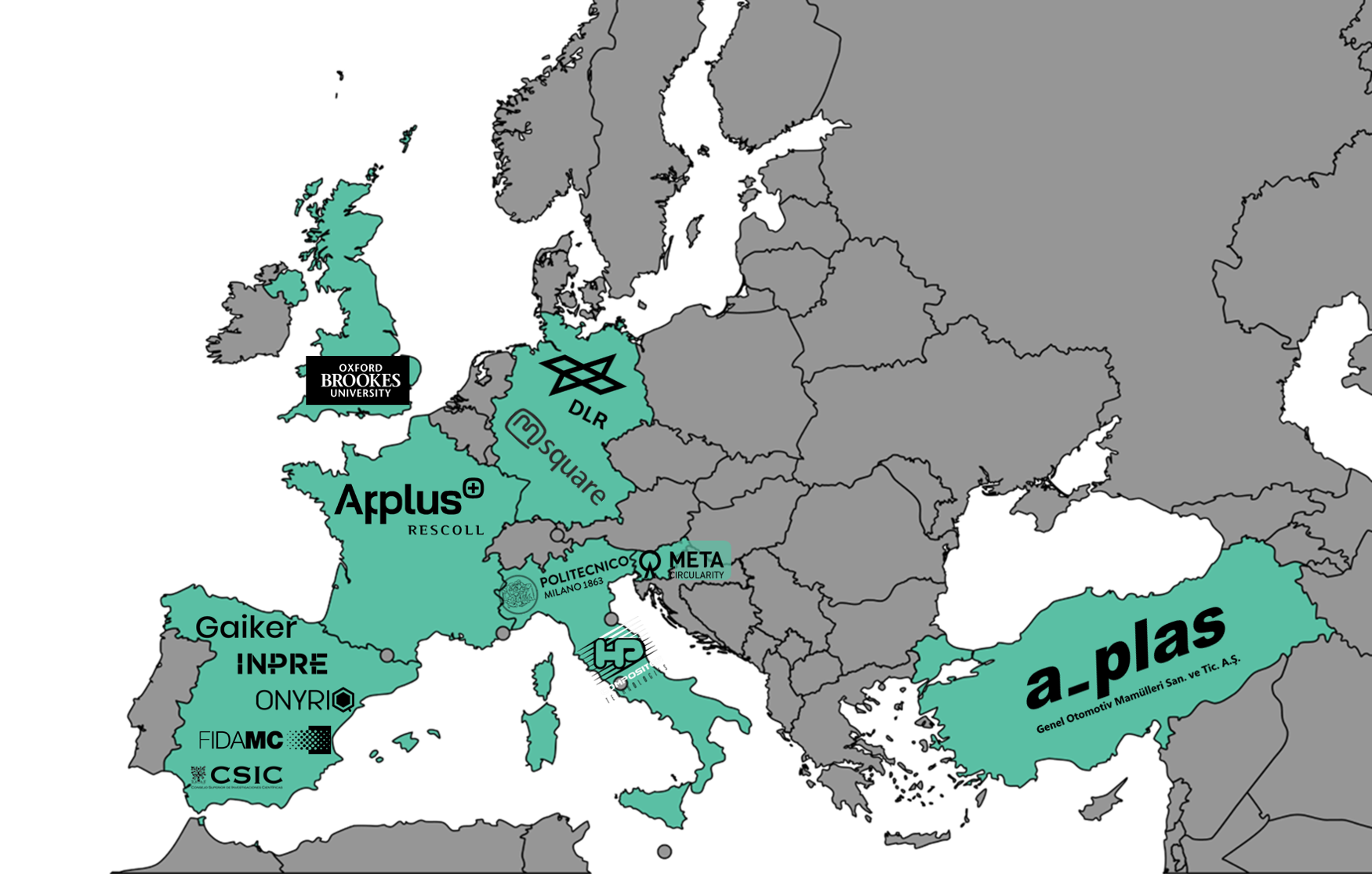
Meet the Consortium
Fundacion GAIKER (Coordinator) – Spain
Fundacion para la Investigacion, Desarrollo y Aplicacion de Materiales Compuestos (FIDAMC) – Spain
Agencia Estatal Consejo Superior de Investigaciones Científicas (CSIC) – Spain
Politecnico di Milano (POLI) – Italy
Onyriq Labs (ONY) – Spain
Applus RESCOLL (RSC) – France
Deutsches Zentrum für Luft und Raumfahrt (DLR) – Germany
Meta Circularity Ltd (MCIRC) – Slovenia
High Performance Composites (HPC) – Italy
Msquare GmbH (M2) – Germany
Oxford Brookes University (OBU) – United Kingdom
A-PLAS (APL) – Turkey
GAIKER, member of Basque Research and Technology Alliance, BRTA, is a Technology Centre located in the Technological Park of Bizkaia (Spain) devoted to research and the provision of innovative technological solutions to companies from sectors such as the environment, chemistry, recycling, transport, construction, among others. From 1985, the Centre has carried more than 2,400 R&D Projects related to its fields of specialisation: Sustainable Composites 4.0, Functional and Sustainable Polymers, Recycling and Circular Economy and Biotechnology. Besides its activity in R&D, GAIKER provide advanced technological services and perform laboratory analysis and certification tests. GAIKER, which boasts a team of more than 100 professionals and the most cutting-edge equipment, have numerous accreditations and certifications that guarantee the rigour and quality of its work. ECORES WIND project give us the opportunity to continue working with sustainable solutions, in this case for the wind energy sector. Gaiker will be engaged in various activities, such as, materials cahracterization, manufacturing processes, and EoL activities. |
FIDAMC is a Research Center created in 2006 by the Spanish Ministry of Industry, the Regional Government of Madrid and the Airbus Group, focused on the research, development and potential uses of composite materials. The entity is mainly addressed to aerospace activities but widely open to other sectors, having carried out projects in the railway, wind energy and automotive areas. FIDAMC facilities are placed in Getafe, with an area of about 1500 m2 for offices and about 4000 m2 for laboratories and workshop. FIDAMC is mainly focused on the improvement of technologies already known and the analysis, test and demonstration of emerging technologies and the selection of the optimal ways to use those technologies in specific products.
For FIDAMC, the ECORES WIND project represents an opportunity to contribute with a more sustainable composite industry, with reusable and repairable elements, with a longer lifespan and a circular life cycle. In order to serve as a link between the Academic and Industrial worlds, FIDAMC role is to help main composite users to adopt these new materials.
The Spanish National Research Council (CSIC) is the largest public research organization in Spain, the fourth largest public research organization in the European Union and the sixth largest in the world. The CSIC is composed of 121 institutes that carry out research, innovation and training in all fields of knowledge. The Instituto de Ciencia y Tecnología de Polímeros (ICTP) (http://www.ictp.csic.es/ICTP2/) focuses on the scientific and technological advancement of polymer materials through research and development. The Polymer Composite Group (PCG) (http://pcg.ictp.csic.es/) is an internationally recognized group in the field of composite materials. The group’s activity is twofold: on the one hand, it develops the fundamental science that applies the tetrahedron of materials to composites: processing, structure, properties and performance. On the other hand, the group develops applied research with a strong interest in knowledge and technology transfer to the industrial sectors. CSIC has developed at laboratory scale a novel thermoplastic liquid resin, called Akelite, which allows the production of high quality composites under a controlled and safe polymerization reaction at medium temperatures and the recovery of both polymer and fibres under good conditions. The objective of the ECORES WIND project is to improve the current Akelite formulation to obtain key properties such as a higher glass transition temperature, currently at 100 C, to finely control the reactivity, and ultimately to enable the disassembly of wind turbine blades, thus contributing to sustainable lifecycle management. |
Politecnico di Milano (POLI) is the 1st public technical university in Italy, and in the world top 20 in the area “Engineering” (https://www.topuniversities.com/universities/politecnico-di-milano). POLIMI has seven campuses located in Milan and in other nearby Italian cities. It is organised in 12 Departments, devoted to research and in 4 Schools, devoted to education. POLIMI has a well-established and documented experience as participant and coordinator of EU-funded research projects.
The POLIMI unit is based within the Department of Chemistry, Materials and Chemical Engineering “Giulio Natta” (www.cmic.polimi.it/en). The research unit possesses a strong long-lasting experience in the field of polymer and composite science, macromolecular chemistry and materials characterization, physical chemistry of surfaces and interfaces, as well as rheology. More specifically, current activities involve the design, development and characterization of polymeric and composite materials for advanced and sustainable manufacturing, and for the circular economy. The POLIMI research unit is fully equipped with an extensive range of facilities for the synthesis, characterization and testing of polymeric and composite materials that will be fully exploited during the project. In addition, the research unit has also access to compounding, molding and recycling facilities for application in the field of polymers and polymer-based composite materials. POLIMI activities within ECORES WIND will be focused on the development of a new class of biobased resin for the future generation of sustainable wind blades.
Onyriq (ONY) develops new, easily industrialized polymers and processes to solve industrial needs in a technical and economically feasible way. With more than 15 years of experience, they have studied the relation between polymeric structures and their physical and chemical properties. They are experts designing and synthesizing polymer materials that meet market’s demands. Onyriq has developed the LOOP technology, consisting of depolymerisable epoxy systems that allow the recovery of reactive building blocks to obtain thermosets in a closed or open cycle. ONYRIQ’s role in the ECORES project will be that of a materials developer researching new compositions of its loop technology to be adapted to the wind turbine blade sector, in terms of process requirements and performance during use. All this, enabling a second life after its useful life has come to an end through the chemical recycling of its resins. |
Applus RESCOLL (RSC) is an innovative French SME, member of the APPLUS+ international group. RESCOLL is conducting innovation research in the field of industrial applications of polymers (composites, resins, adhesives, varnish, coatings, etc.) and related fields: bonded assemblies, materials for fire behavior and environmentally friendly surface treatments. RESCOLL does more than 45% of its sales in the aerospace industry. The company has been at the origin of more than 40 patents in the field of polymers and composites. RESCOLL has ISO 17025 and NADCAP accredited laboratories and is specialized in the fields of polymer formulation, vibroacoustic testing, mechanical characterization, non-destructive control, fire testing, thermo mechanical analysis, spectrometry and chromatography and surface analysis and accelerated ageing. RESCOLL has worked extensively on the development of advanced surface coating and bonding technologies and has equipped a laboratory specifically for studies related to surface characterization and analysis. Thanks to projects supported on both the national and European level, RESCOLL has a team who has a great deal of experience in the development of debondable adhesion coatings. RESCOLL’s INDAR INSIDE debondable adhesives and primers have already seen application in numerous applications, including textile and the automotive sector. In ECORESWIND, APPLUS+ Rescoll will develop a new range of dedicated bonding systems consisting of its patented technology INDAR debondable primer, associated with commercial adhesives generally used in the wind energy sector. |
Deutsches Zentrum für Luft und Raumfahrt (DLR) is the German aerospace research and technology centre. It mainly develops technologies for aeronautics and space, energy and transport, as well as security and defence research. Over 11,000 employees in 54 research institutes and facilities at 30 locations are creating solutions for a sustainable future. Two DLR project management organisations work as management facilities for research and industry funding. The German Space Agency at DLR is responsible for the planning and implementation of German space activities on behalf of the Federal Government.
The DLR Institute of Lightweight Systems develops and tests new lightweight construction technologies for resource-saving and climate-friendly structures in the aerospace, transport, energy and security sectors. Our vision is intelligent lightweight system for an emission-free tomorrow, based on three pillars: lightweight material construction, lightweight design and functional integration. Our research portfolio includes high-performance materials, analysis methods for the entire life cycle, function-integrating lightweight constructions, efficient manufacturing processes for fibre composite structures on an industrial scale, adaptive structural systems and the end-to-end digitalisation of the entire process chain. We operate extensive testing facilities to clarify issues relating to material properties, stability, strength and the thermal and acoustic behaviour of components and parts.
The business area Wind is where the institute pools its expertise in the field of wind energy. The focus is primarily on the rotor blades of modern wind turbines. The research topics in this business area range from service life-optimised or functionalised materials, optimised design and new construction methods to quality-controlled production. Aspects of recycling are taken into account in all product life cycle phases in order to further increase the sustainability of wind energy. Life cycle analyses are used to carry out both economic and ecological assessments of the technologies.”
META Circularity (MCIRC) is a knowledge-focused consultancy focused on meaningful, sustainable corporate transformations, strategic communication and stakeholder development, especially in the context of innovation and circular transition. We transform business models and brands into more sustainable and more circular considering competence and experience acquired in the field of business model transformations, innovation management, journalism and media, social innovation and service design.
We are particularly dedicated to creating sustainable, innovative business models and promoting the transition to the circular economy. We advise, train and support business partners on how to manage the transformation processes of their business models and integrate them into circular value chains. In doing so, we advocate for a systematic approach to the transition to the circular economy and promote circular culture.
META Circularity is the carrier of the Circular Business Academy (CBA), a platform that brings together various forms of training and education for professionals, decision-makers and contractors, companies and other organisations in any sector to accelerate circular transformation.
In the ECORES WIND initiative we are a leader of communication, dissemination and exploitation activities.
High Performance Composites (HPC) has always prioritised care of social, environmental, and economic sustainability. They are currently producing wind blades, boat parts and other composite components, using durable and low inpact materials with minimum waste. In ECORES WIND HPC is committed to pursuing a regenerative production model that adopts the principles of a circular economy by providing grounds for demonstration of developed technologies in the project. |
MSQUARE GmbH (M2) is an innovative technology company specializing in the development of advanced repair technologies and novel concepts for the wind energy sector. Our core expertise lies in providing cutting-edge solutions to enhance the lifecycle and performance of wind turbines by focusing on the sustainability and efficiency of composite materials. Our team is dedicated to revolutionizing the way wind turbines are maintained by introducing state-of-the-art techniques for repairing and extending the durability of composite structures, including wind blades. Our motivation to join the ECORES WIND project stems from our commitment to promoting circularity and minimizing the environmental impact of the wind energy industry. By collaborating with leading industry and research partners, we aim to contribute to the development of circular resin systems and reversible adhesives that will significantly enhance the recyclability and reusability of wind turbine components. This aligns with our vision of creating sustainable, cost-effective, and innovative solutions for wind energy applications. Through our participation in ECORES WIND, we aspire to play a pivotal role in advancing repair and recycling technologies that support the renewable energy sector, ensuring a greener, more efficient future for wind energy systems. |
Researchers at Oxford Brookes University (OBU) have extensive prior experience on both the technical aspects of new resins and reversible bonding techniques to facilitate end-of-life disassembly and recycling, and on cradle-to-grave full life cycle assessment (LCA) of rewewable energy systems. This places them in the ideal position to be able to assess the potential offered by the new resins being investigated within the ECORES WIND project in terms of improving the whole life-cycle environmental performance of Wind power systems, in terms of a number of independent impact categories. The ultimate aim of our work within the project is to provide an independent and unbiased assessment of the potential of wind energy, which can be used to inform future policy scenarios for electricity grid mix decarbonization.
A-plas Genel Otomotiv Mamulleri San. Tic. A.Ş. (APL) in three different locations in total 48.000 m2 area with 650 employees using the latest technologies in all production lines, which are plastic injection, extrusion, blow molding, ultrasonic welding, painting, chrome electroplating etc, produces interior, exterior and under hood plastic parts. A-plas is serving with 65 injection machines from 110 tons to 3200 tons in plastic production lines, 11 blow molding machines in blow molding lines and as additional two robotic, one manual paint lines and one chrome electroplating line in the automotive industry. The parts that are produced to OEMs by A-plas are delivered to the leading companies of the automotive industry that are located in North America, England, Spain, Germany, Slovakia, Czech Republic, Poland, Brazil, Russia, India etc. Since its establishment, A-plas has developed many projects for the first time in Turkey that some of these are bumper tool production with local toolmakers and bumper delivery with JIS system, C02 cleaining before painting application, chrome electroplating and hot stamping diamond grill effect on radiator grills. A-plas is serving as a FSS (full service supplier) and co-design supplier, within this scope our chemistry lab, physics lab, chrome lab and paint laboratories are accredited by OEMs. A-plas laboratories have capability for making all product and process tests in the product development process. Our Government supported R&D Center was established in 2019. All design and simulation activities can be handled by R&D department. The second life application of the ECORES-WIND project will be in the A-PLAS production lines. Recycled resins will tried to be transformed to industrial products by Plastic Injection Process. A-PLAS will also provide feedback from the field during the development phase of the resin. |
INPRE COMPOSITES (INP) was founded in 1988, as the first Spanish composites company dedicated to the manufacture of GRP/FRP (Fiberglass Reinforced Polyester) laminates in rolls/coils for the European industrial bodywork market under the MODULCAR brand.
In 1995, INPRE began its wind activity, supporting GAMESA EÓLICA in the manufacturing and development of GRP/FRP canopies and spinners for wind turbines. Starting on drawings & specifications, INPRE develops the production process, supply chain management and final assembly, following the strictest quality standards. Besides INPRE assembles and integrates wind turbine components according to customer requirements
The INPRE team is formed by professionals with extensive experience in techniques for the manufacturing of GRP components such as RTM, infusion, etc. INPRE has its own laboratory, and technicians and engineers are always aware of new raw materials and their possible applications in the composites market. INPRE specialised technical personnel is distributed in 3 main areas: R&D, Quality Lab and New Projects & Moulds.
INPRE is a highly committed company in the reduction of its carbon footprint with initiatives such as the ECOVADIS Silver label. Being a partner in ECORES WIND will allow INPRE not only to be ahead in the know-how of the latest advances in this field but also to contribute to the development of new composites by providing input on the market requirements and a possible use of the products developed during the project.